Funding Phase II
Reliability is a decisive factor in the context of adaptive load-bearing structures in civil engineering with regard to the behavior of the structure in the event of a partial or complete failure of the actuator, sensor or control system. The influence of wear or fatigue of notch points of the structure as well as the effect of failures on the operation must be considered. This leads to the central questions of this subproject, which concern the analysis of redundancies in structural topologies, the detection of failure cases as well as lifetime monitoring to maintain ultimate limit and serviceability limit states.
In order to ensure ultimate limit and serviceability limit state of the structure, even in the event of actuator, sensor and control failures, the influence of the structure’s topology and the position of the actuators is investigated. In addition, the question is addressed on how adaptive structures have to be designed, so that they are still stable with failed actuators and whether the structure can be brought into a safe state, e.g. by stored passive energy or deliberate additional dissipation.
The detection and isolation of fault cases in actuators, sensors and the structure form the basis for ensuring ultimate limit and serviceability limit states through appropriate measures. In the previous funding period, it was shown that the number and placement of sensors has a significant influence on the detectability and distinguishability of fault cases. Therefore, quality measures and methods regarding the placement of actuators and sensors are developed, which ensure a high fault tolerance as well as a good detectability and distinguishability of fault cases for the subsequent fault diagnosis. In order to ensure the scalability of fault diagnosis to large and complex structures and to keep the application effort manageable, decentralized and modular approaches based on model- and data-based methods for the detection and isolation of actuator, sensor and structural faults will be developed and applied to different types of structures based on the results of the previous funding period. While decentralized fault diagnosis derives subsystems based on an overall model of the structure, modular fault diagnosis is based on local models of the individual modules, resulting in good reusability of the module models and low application effort since no overall model for the structure needs to be set up. The unknown system couplings between the modules are a challenge for the individual fault diagnosis systems.
While in the first funding period the focus was on the design of adaptive load-bearing structures, monitoring the service life and the resulting overall structural properties, such as ultimate limit and serviceability limit states, in operation is of major importance. For this purpose, in this funding period the stresses are monitored online. In addition to the visualization of critical components, online monitoring allows the realization of an operating strategy that pursues the control objective of homogenized wear. In this way, maintenance- and service-life-optimized operation is achieved while maintaining structural reliability and optimize sustainability. In this context, spare parts demand and structural service life influence the environmental impact, which is why this interaction is included. In addition, research is being conducted into how redundancies, present in the topology of the load-bearing structure can be considered in the reliability assessment.
The following main aspects of the subproject emerge:
- Identification of the influence of the topology of an adaptive load-bearing structure and the location of the actuators on the serviceability limit state and the load-bearing capacity.
- Development of technical concepts to ensure stability in case of total failure of the actuators
- Development of concepts for actuator and sensor placement for fault diagnosis in structures or structural modules
- Development, combination and generalization of model- and data-based methods for decentralized, modular and active fault diagnosis
- Lifetime prediction and active lifetime management with predictive maintenance using the available actuators and sensors of adaptive load-bearing structures
- Identify and combine reliability and sustainability goals with consideration in an optimal operational strategy
Regelkreis des Prognostics and Health Management
Lebensdauermanagement durch Eingriff in die Betriebsstrategi
Subproject Leader
- Prof. Dr.-Ing. Cristina Tarín, Institute for System Dynamics
- Prof. Dr.-Ing. habil. Manfred Bischoff, Institute for Structural Mechanics
- Dr.-Ing. Martin Dazer, Institute of Machine Components
Funding Phase I
Malfunctions and failures within the adaption process are harmful for the overall load-bearing structure or compromise functioning for the user and have to be avoided or rather detected in time. Therefore, if a failure occurs it may not have fatal consequences.
Foto: (c) ILEK
For this reason project B03 examines uncertainties, disturbances, faults and failure possibilities. An integrated monitoring and fault detection informs about the occurrence of faults. A subsequent fault diagnosis allows conclusions about the fault location, which is used for their isolation and detection at an early stage. To design the system less susceptible to interferences and more robust against disturbances, the disturbances are considered in the fault diagnosis design. For a more sustainable construction, the safety and reliability-oriented design of adaptive load-bearing structures is important. The more precisely the expected operating load is known and considered in the reliability model, the more accurately the load-bearing structure is designed. Uncertainties caused by failures of the adaptive function must be avoided by a functionally safe system, in which diagnostics in turn play an important role.
Summarized this yields to the following essential questions:
- Which fauls and loads are characteristic for adaptive structures and how can they be modelled?
- Which load spectra lead to failure-critical states and what is the relationship to serviceability and ultimate limit state of adaptive structures?
- How can this relationship be modelled considering failures in the adaptation process?
- How can faults be distinguished from unknown loads and reliably detected and isolated?
- Which methods are suitable for fault detection and diagnosis in adaptive structures?
- Which failure reactions are necessary to avoid fatal faults?
- How do safety, reliability and sustainability of adaptive structures influence each other and how can a comprehensive design method include these central aspects?
- What are relevant measurement signals for the detection of faults?
The basic objective of the failure detection is the diagnosis of faults in actuators and sensors of adaptive structures which are influenced by stochastic and non measurable loads.
Risk factors of passive and adaptive structures
For fault diagnosis, it must be ensured that the faults are detectable and distinguishable from the loads. For this purpose, criteria are developed which allow the disinguishability between faults and loads as well as the isolation of faults. Model-based and data-based methods are investigated for the detection and isolation of the faults.
Residual values and fault probability for a random walk fault in a strain gauge
The results of the fault diagnosis is passed to the projects B02 and B04 for reconfiguring the observer and controller. C02 is provided with reliability requirements for choosing an actuator concept optimized regarding reliability. For a reliable power supply of the electro active polymers an investigation is handed to C03.
Convolutional neural network for fault classification based on measurement data
n the further course of the project, the influence of the topology and the position of the actuators on the serviceability and load-bearing capacity will be identified and technical concepts will be developed to ensure stability in the event of total failure of the actuators. Furthermore, concepts for actuator and sensor placement with regard to detectability and fault tolerance are developed in cooperation with other subprojects.
Interdisciplinary design method for adaptive structures
The concepts for actuator and sensor placement form the basis for the development of model and data-based approaches for fault diagnosis and generalization to different types of adaptive structures. This will be supplemented by an active fault diagnosis in the actuator system. Furthermore, a Prognostics and Health Management for reliability and sustainability improvement with influence on the actuators is developed.
Subproject Leader
- Prof. Dr.-Ing. Bernd Bertsche, Institute of Machine Components
- Prof. Dr.-Ing. Cristina Tarín, Institute for System Dynamics
Publications
- J. Stiefelmaier, S. Dakova, C. Stein, M. Böhm, C. Tarín, and O. Sawodny, “Reconfiguration of an Adaptive Structure’s Control Loop Based on Diagnosed Sensor and Actuator Faults,” Journal of Structural Engineering, Apr. 2024, doi: 10.1061/JSENDH.STENG-12638.
- L.-M. Krauß et al., “Baustatische Methoden für Entwurf, Auslegung und Betrieb adaptiver Tragwerke,” in Berichte der Fachtagung Baustatik – Baupraxis 15, 04. und 05. März 2024, Hamburg, B. Oesterle, A. Bögle, W. Weber, and L. Striefler, Eds., 2024, pp. 101–108. doi: 10.15480/882.9247.
- L.-M. Krauß et al., “Berichte der Fachtagung Baustatik – Baupraxis 15 : 04. und 05. März 2024, Hamburg.” Institut für Baustatik, Technische Universität Hamburg, 2024. doi: 10.15480/882.9247.
- J. Stiefelmaier, M. Böhm, O. Sawodny, and C. Tarín, “Parity Space-Based Fault Diagnosis in Piecewise Linear Systems,” in IFAC World Congress, 2023. doi: https://doi.org/10.1016/j.ifacol.2023.10.764.
- J. Stiefelmaier, A. Gienger, M. Böhm, O. Sawodny, and C. Tarín, “A Bayesian Approach to Fault Diagnosability Analysis in Adaptive Structures,” in 9th IFAC Symposium on Mechatronic Systems (Mechatronics 2022), IFAC, Sep. 2022.
- D. Efinger, A. Ostertag, M. Dazer, D. Borschewski, S. Albrecht, and B. Bertsche, “Reliability as a Key Driver for a Sustainable Design of Adaptive Load-Bearing Structures,” Sustainability, Art. no. 14(2), 2022, doi: 10.3390/su14020895.
- D. Borschewski et al., “Ökobilanzierung adaptiver Hüllen und Strukturen,” Bautechnik, vol. 99, Art. no. 10, Oct. 2022, doi: 10.1002/bate.202200067.
- S. Dakova, J. L. Heidingsfeld, M. Böhm, and O. Sawodny, “An Optimal Control Strategy to Distribute Element Wear for Adaptive High-Rise Structures,” in American Control Conference (ACC), Atlanta, USA: IEEE, Jun. 2022.
- A. Ostertag, M. Dazer, and B. Bertsche, “METHODE ZUR ZUVERLÄSSIGEN, SICHEREN UND NACHHALTIGEN AUSLEGUNG ADAPTIVER TRAGWERKE,” 2021.
- M. Dazer, A. Ostertag, T. Herzig, D. Borschewski, S. Albrecht, and B. Bertsche, “Consideration of reliability and sustainability in mechanical and civil engineering design to reduce oversizing without risking disasters,” 2021.
- J. Stiefelmaier, A. Gienger, M. Böhm, O. Sawodny, and C. Tarín, “Sensor Placement for Qualitative Fault Diagnosability in Large-Scale Adaptive Structures,” in IEEE International Conference on Mechatronics, Robotics and Systems Engineering, 2021. doi: 10.1109/MoRSE50327.2021.9766016.
- S. Dakova, J. L. Wagner, A. Gienger, C. Tarín, M. Böhm, and O. Sawodny, “Reconfiguration Strategy for Fault-Tolerant Control of High-Rise Adaptive Structures,” IEEE Robotics and Automation Letters, vol. 6, Art. no. 4, 2021.
- A. Gienger, “Ansätze zur Kombination modell- und datenbasierter Methoden für die Prozessüberwachung und Fehlerdiagnose,” 2021.
- A. Gienger, J. Wagner, M. Böhm, O. Sawodny, and C. Tarín, “Robust Fault Diagnosis for Adaptive Structures With Unknown Stochastic Disturbances,” IEEE Transactions on Control Systems Technology, 2020, doi: 10.1109/TCST.2020.2993068.
- A. Ostertag et al., “Reliable design of adaptive load-bearing structures with focus on sustainability,” 2020. doi: 10.3850/978-981-14-8593-0_3806-cd.
- A. Gienger, S. Schaut, O. Sawodny, and C. Tarín, “Modular Distributed Fault Diagnosis for Adaptive Structures using Local Models,” in Proc. of the IFAC World Congress, 2020.
- A. Gienger, A. Ostertag, M. Böhm, B. Bertsche, O. Sawodny, and C. Tarín, “Data-Based Distributed Fault Diagnosis for Adaptive Structures using Convolutional Neural Networks,” Unmanned Systems, 2020, doi: 10.1142/S2301385020500156.
Contact

Jonas Stiefelmaier
M.Sc.Doctoral Researcher
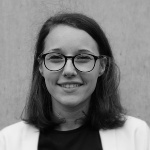
Tamara Prokosch
M. Sc.Doctoral Researcher
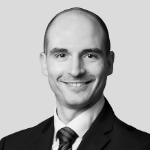
Dshamil Efinger
M.Sc.Doctoral Researcher